hydraulic symbols pdf
- by gage
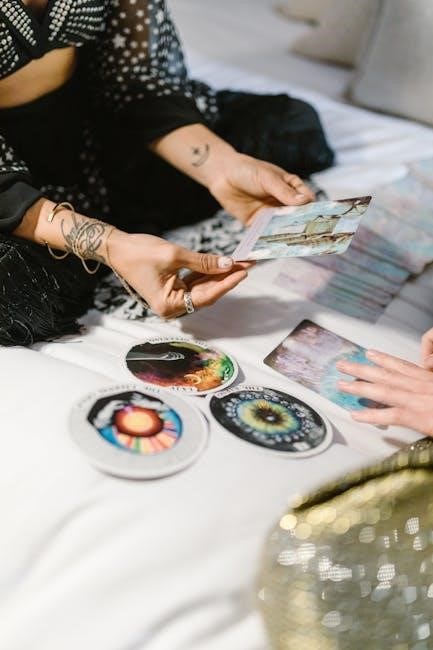
Hydraulic symbols are standardized graphical representations used to design and understand hydraulic systems. They ensure universal communication in engineering, covering components like pumps, valves, and cylinders. These symbols, governed by standards such as ISO 1219-1 and ANSI Y32.10, are essential for creating clear and functional hydraulic circuit diagrams.
- They represent components and their functions in hydraulic circuits.
- Standardization ensures consistency across industries worldwide.
- They are used in industrial machinery, mobile hydraulics, and aerospace engineering.
1.1 Definition and Importance
Hydraulic symbols are standardized graphical representations used to depict components and their functions in hydraulic systems. They are essential for clear communication, ensuring consistency and accuracy in system design, installation, and maintenance. These symbols are critical for avoiding errors, enhancing safety, and facilitating efficient troubleshooting in hydraulic circuits.
- They standardize communication across industries.
- They simplify complex system designs.
- They reduce the risk of operational errors.
1.2 Brief History and Evolution
Hydraulic symbols originated from early engineering practices, evolving to standardize communication in fluid power systems. The establishment of ISO 1219-1 and ANSI Y32.10 standards formalized these symbols, ensuring consistency and clarity. Over time, updates have incorporated new technologies and components, reflecting industry advancements and the growing complexity of hydraulic systems.
- Early symbols were basic and varied.
- Standardization began in the mid-20th century.
- Continuous updates reflect technological progress.
Standardization of Hydraulic Symbols
Standardization ensures consistency in hydraulic symbols, enabling universal understanding. ISO 1219-1 and ANSI Y32.10 are key standards, providing clear guidelines for symbol design and application.
- Promotes clarity in system design.
- Enables precise communication among engineers.
- Facilitates global compatibility and collaboration.
2.1 ISO 1219-1:2012 Standard
The ISO 1219-1:2012 standard specifies graphical symbols for hydraulic systems, ensuring consistency and clarity. It covers components like pumps, valves, and actuators, providing detailed representations for circuit diagrams. This standard facilitates international communication, making it a cornerstone in hydraulic system documentation and design.
- Covers both hydraulic and pneumatic symbols.
- Provides universal interpretation of components.
- Enhances design and troubleshooting efficiency.
2.2 ANSI Y32.10 Standard
The ANSI Y32.10 standard provides graphical symbols for fluid power systems, including hydraulics and pneumatics. It ensures uniformity in representing components like pumps, valves, and cylinders. This standard aids in creating clear circuit diagrams, facilitating design, installation, and maintenance across industries in the United States.
- Specifies symbols for fluid power systems.
- Ensures consistency in system documentation.
- Facilitates efficient communication among engineers.
Basic Hydraulic Symbols
Basic hydraulic symbols represent fundamental components and lines in hydraulic systems. They include supply and return lines, pilot lines, and flexible hoses, providing a visual language for system design and functionality.
- Supply lines indicate fluid flow to components.
- Return lines show fluid flow back to reservoirs.
- Pilot lines control directional valves.
3.1 Supply and Return Lines
Supply and return lines are essential in hydraulic systems, represented by solid and dashed lines respectively. Supply lines deliver pressurized fluid to components, while return lines direct de-energized fluid back to the reservoir. These lines form the backbone of hydraulic circuits, ensuring efficient fluid flow and system functionality.
- Supply lines are typically solid, indicating pressurized fluid flow.
- Return lines are dashed, showing de-energized fluid returning to the reservoir.
3.2 Pilot and Drain Lines
Pilot and drain lines are crucial for controlling hydraulic systems. Pilot lines regulate valve operations, while drain lines direct fluid from components back to the reservoir. These lines ensure precise control and system efficiency, preventing contamination and maintaining hydraulic fluid integrity.
- Pilot lines control valve operations with low-pressure fluid.
- Drain lines safely return used fluid to the reservoir.
3.3 Flexible Hose and Connections
Flexible hoses and connections provide adaptability in hydraulic systems, allowing movement and vibrations. They are represented by specific symbols, indicating their function and flexibility. Proper use ensures system integrity, accommodating varying pressures and flows while maintaining reliability.
- Flexible hoses connect components, absorbing vibrations and enabling movement.
- Their symbols denote flexibility and connection types in diagrams.
Hydraulic Pumps and Motors
Hydraulic pumps convert mechanical energy into hydraulic energy, driving system operations. Fixed and variable displacement pumps offer versatility, while motors transform hydraulic energy back into mechanical energy efficiently.
- Fixed displacement pumps maintain constant flow rates.
- Variable displacement pumps adjust flow based on demand.
- Hydraulic motors provide precise control over movements.
4.1 Fixed Displacement Pumps
Fixed displacement pumps deliver a constant volume of fluid per cycle, ensuring steady flow rates. Their simple design makes them reliable and cost-effective for applications where consistent pressure is required. These pumps are ideal for systems with minimal flow variations, providing predictable performance in various hydraulic applications.
- Constant flow rate regardless of system pressure.
- Simple and durable construction.
- Commonly used in industrial machinery.
4;2 Variable Displacement Pumps
Variable displacement pumps adjust the fluid volume per cycle, offering flexibility in flow rate and pressure. They are controlled mechanically, hydraulically, or electronically, making them suitable for systems requiring variable output. These pumps enhance efficiency by matching output to demand, reducing energy consumption in dynamic applications.
- Adjustable displacement for variable flow rates.
- Efficient in systems with changing demands.
- Controlled via mechanical, hydraulic, or electronic means.
4.3 Hydraulic Motors
Hydraulic motors convert hydraulic energy into mechanical energy, driving rotational motion in systems. They are categorized as fixed or variable displacement, operating bidirectionally or unidirectionally. Motors are essential in applications requiring precise speed and torque control, commonly used in industrial machinery, mobile equipment, and aerospace systems for reliable performance under varying loads.
- Convert hydraulic pressure into mechanical rotation.
- Available in fixed or variable displacement types.
- Used for precise speed and torque control.
Hydraulic Valves
Hydraulic valves control fluid flow, pressure, and direction in hydraulic systems. They are essential for regulating system performance, ensuring efficiency, and maintaining safety. Key types include pressure control, directional, and flow control valves, each serving specific functions to manage hydraulic energy effectively.
- Regulate fluid flow and pressure in hydraulic circuits.
- Ensure system efficiency and operational safety.
- Available in pressure, directional, and flow control types.
- Regulate and limit pressure in hydraulic circuits.
- Protect components from excessive pressure damage.
- Ensure system stability and operational safety.
- Control fluid flow direction between system components.
- Operate manually or through electrical solenoids.
- Critical for precise actuator and motor control.
- Regulate fluid flow rate and pressure to prevent system damage.
- Essential for maintaining optimal hydraulic circuit performance.
- Available in various types to suit specific operational needs.
- Key components include piston, rod, and fluid chambers.
- Used for linear motion in hydraulic systems.
- Symbols are standardized for universal understanding.
- Hydraulic pressure extends the piston and rod.
- Retraction occurs via external forces like springs or loads.
- Commonly used in applications requiring simple, cost-effective solutions.
- Hydraulic pressure powers both extension and retraction.
- Features rods on both ends of the piston.
- Ideal for applications needing precise, reversible motion.
- Nested piston rods enable extended reach in limited space.
- Symbol shows multiple concentric circles for each stage.
- Used in cranes, excavators, and lifting equipment.
- Accumulators store energy for emergency or peak demand situations.
- Heat exchangers maintain optimal fluid temperatures.
- Pressure intensifiers amplify pressure for specialized operations.
- Store energy for system stabilization and backup.
- Reduce pressure fluctuations and system shock.
- Enhance overall hydraulic system efficiency and reliability.
- Prevent overheating of hydraulic fluids.
- Protect components from thermal damage.
- Ensure reliable system performance and durability.
- Amplify hydraulic pressure for specific tasks.
- Used in metal forming and injection molding.
- Available in hydraulic or mechanical designs.
- Visual representation of hydraulic systems.
- Essential for design and maintenance.
- Use standardized symbols for clarity.
- Understand component symbols and their functions.
- Identify fluid flow paths and connections.
- Recognize directional arrows and pressure levels.
- Open circuits: Fluid flows from reservoir to component and back.
- Closed circuits: Fluid continuously recirculates.
- Symbols simplify understanding of flow paths and controls.
- Use standardized symbols for clarity and consistency.
- Organize components in a logical flow sequence.
- Label all connections and pressure points clearly.
- Essential for industrial machinery design and maintenance.
- Crucial in mobile hydraulics for vehicle systems.
- Utilized in aerospace for precise system control.
- Used in designing and maintaining industrial equipment.
- Ensure clarity in fluid power system operations.
- Enhance safety and efficiency in manufacturing processes.
- Essential for designing and maintaining mobile hydraulic systems.
- Enable clear understanding of fluid power in vehicles.
- Enhance safety and performance in construction and agricultural equipment.
- Essential for designing complex aerospace hydraulic systems.
- Enable precise communication among engineers and technicians.
- Critical for ensuring reliability in aircraft operations.
- Mastering hydraulic symbols enhances system design and troubleshooting.
- Utilize standardized resources for accurate interpretations.
- They represent components and their functions in hydraulic circuits.
- Standardization ensures consistency across industries worldwide.
- They are used in industrial machinery, mobile hydraulics, and aerospace engineering.
5.1 Pressure Control Valves
Pressure control valves regulate hydraulic system pressure by directing fluid flow from high-pressure areas to low-pressure zones. They ensure system stability and protect components from over-pressurization, operating automatically or manually. These valves are crucial for maintaining safe and efficient hydraulic operations across various applications.
5.2 Directional Control Valves
Directional control valves regulate fluid flow direction in hydraulic systems, enabling precise control of actuator movements. They operate via solenoids, manual levers, or pilot lines, directing fluid to specific ports. These valves are essential for system functionality, ensuring accurate operation of hydraulic components like cylinders and motors.
5.3 Flow Control Valves
Flow control valves regulate the flow rate and pressure in hydraulic circuits, ensuring system efficiency and safety. They prevent damage by controlling fluid velocity and pressure spikes. Common types include throttle, pressure-compensated, and priority valves, each designed for specific applications in industrial and mobile hydraulic systems.
Hydraulic Cylinders
Hydraulic cylinders convert hydraulic energy into mechanical energy, enabling linear motion in systems. They consist of a piston, rod, and chambers. Standardized symbols represent their function and configuration, ensuring clarity in hydraulic circuit diagrams.
6.1 Single-Acting Cylinders
A single-acting cylinder operates with hydraulic pressure to extend the piston and rod, relying on an external force, such as a spring or load, for retraction. Its symbol features a piston with a rod on one side and a spring or external force on the other, indicating unidirectional hydraulic actuation.
6.2 Double-Acting Cylinders
A double-acting cylinder uses hydraulic pressure to extend and retract the piston and rod, enabling bidirectional operation. Its symbol shows a piston with rods on both sides, indicating hydraulic actuation in both directions, commonly used in applications requiring precise control and continuous motion, such as excavators and lifting equipment.
6.3 Telescopic Cylinders
Telescopic cylinders are multi-stage cylinders with nested piston rods, allowing for extended reach in compact spaces. Their symbol depicts concentric circles representing each stage. They are ideal for applications like cranes and excavators, where space is limited but long strokes are required. Each stage extends sequentially to achieve maximum extension while retracted neatly when not in use.
Hydraulic Actuators and Ancillaries
Hydraulic actuators and ancillaries are essential components that enhance system efficiency, safety, and performance. They include accumulators for energy storage, heat exchangers for temperature control, and pressure intensifiers for boosting pressure in specific applications.
7.1 Hydraulic Accumulators
Hydraulic accumulators store pressurized fluid energy for system stabilization and emergency power supply. They buffer pressure fluctuations, provide backup during power failures, and enhance system efficiency. Common types include piston, bladder, and diaphragm accumulators, each designed for specific applications.
7.2 Heat Exchangers and Coolers
Heat exchangers and coolers are essential for maintaining optimal hydraulic system temperatures. They dissipate heat generated by pump and motor operations, preventing oil degradation and system damage. Common types include plate, shell, and tube heat exchangers, designed to ensure efficient thermal management and system longevity.
7.3 Pressure Intensifiers
Pressure intensifiers amplify hydraulic pressure for specialized applications, converting lower pressure to higher pressure. They are typically used in metal forming or injection molding. These devices can be hydraulic or mechanical, ensuring precise control over pressure levels in demanding operational environments.
Hydraulic Circuit Diagrams
Hydraulic circuit diagrams visually represent system components and their connections, using standardized symbols. They are crucial for designing, troubleshooting, and maintaining hydraulic systems efficiently.
8.1 Reading and Interpreting Diagrams
Reading hydraulic circuit diagrams involves understanding standardized symbols and their connections. Each symbol represents a component, such as pumps, valves, or cylinders, while lines indicate fluid flow paths. Directional arrows show flow direction, and colors may denote pressure levels. Accurate interpretation is crucial for troubleshooting, maintenance, and system optimization.
8.2 Common Circuit Configurations
Common hydraulic circuit configurations include open and closed systems. Open circuits transfer fluid from a reservoir to a component and back. Closed circuits continuously recirculate fluid. Symbols clearly depict these setups, ensuring proper understanding of flow paths, pressure control, and component interactions. Standard configurations enhance system efficiency and simplify troubleshooting.
8.3 Best Practices for Diagram Creation
Best practices for creating hydraulic diagrams include using standardized symbols, organizing components logically, and clearly labeling connections. Start with a list of components and their functions. Use ISO 1219-1 guidelines for consistency. Color-code lines for pressure, return, and pilot flows. Regularly review and update diagrams to reflect system changes and ensure accuracy.
Applications of Hydraulic Symbols
Hydraulic symbols are widely used in industrial machinery, mobile hydraulics, and aerospace engineering to design and maintain fluid power systems. They ensure clear communication among engineers and technicians, facilitating efficient system operation and troubleshooting.
9.1 Industrial Machinery
Hydraulic symbols are integral to industrial machinery, enabling clear communication in system design and maintenance. They represent components like pumps, valves, and cylinders, ensuring efficient operation and troubleshooting. Standardized symbols aid engineers in understanding complex fluid power systems, enhancing productivity and safety across manufacturing and heavy industries.
9.2 Mobile Hydraulics
Hydraulic symbols are crucial in mobile hydraulics, used in vehicles and equipment like excavators and cranes. They ensure proper system design, operation, and maintenance. Symbols for components such as hoses, pumps, and valves aid technicians in understanding fluid flow and pressure control, enhancing efficiency and reliability in mobile applications.
9.3 Aerospace Engineering
Hydraulic symbols play a vital role in aerospace engineering, where precise system design is critical. They are used to represent hydraulic components like pumps, valves, and actuators in aircraft systems. Standardized symbols ensure clarity in designing and maintaining hydraulic systems for landing gear, flight control surfaces, and utility systems, enhancing safety and efficiency.
Hydraulic symbols are essential for designing and interpreting fluid power systems. For further learning, refer to ISO 1219-1 and ANSI Y32.10 standards, and visit abdex.com for detailed guides.
10.2 Recommended Reading and Tools
10.1 Summary of Key Points
Hydraulic symbols are standardized graphical representations used to design and interpret fluid power systems. They ensure universal communication in engineering, covering components like pumps, valves, and cylinders. These symbols, governed by standards such as ISO 1219-1 and ANSI Y32.10, are essential for creating clear and functional hydraulic circuit diagrams.
Related posts:
Find hydraulic symbols in PDF format! Download free guides, charts, and diagrams for your engineering projects. Get instant access now!
Posted in PDF