prensa hidraulica manual
- by gage
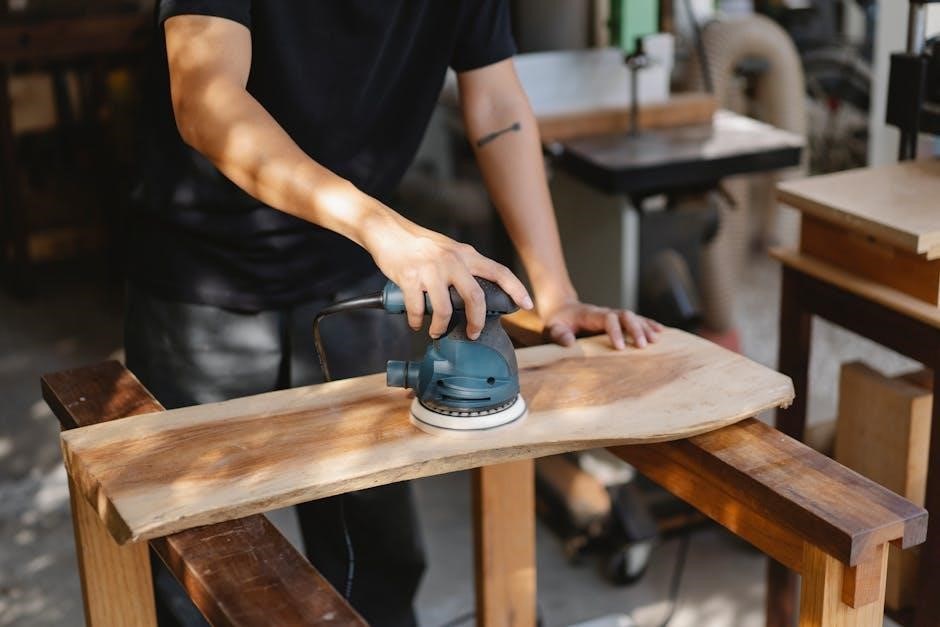
A manual hydraulic press is a compact, portable tool that uses hydraulic pressure to apply force for pressing, shaping, or assembling parts, ideal for various industrial applications․
What is a Manual Hydraulic Press?
A manual hydraulic press is a tool that uses hydraulic pressure to apply force for pressing, shaping, or assembling parts․ It is operated manually, often using a handle or lever to generate pressure through a hydraulic system․ This tool is commonly used in metalworking, plastics processing, and other industries requiring precise force application․ Its design typically includes a frame, hydraulic cylinder, and pump, making it portable and suitable for workshops or small-scale operations․ The manual operation allows for control and versatility, catering to various industrial needs․
History and Evolution of Hydraulic Presses
The manual hydraulic press traces its origins to the late 18th century, when Joseph Bramah invented the first practical hydraulic press․ Initially used for pressing and shaping metal, its design evolved over time to become more portable and versatile․ By the 20th century, manual versions emerged, offering compact solutions for smaller-scale operations․ Modern manual hydraulic presses incorporate lightweight materials and advanced sealing technologies, enhancing durability and efficiency while maintaining their core functionality for precise force application in various industrial settings․
Types of Manual Hydraulic Presses
Manual hydraulic presses are categorized into hand-operated and foot-operated models, each designed for specific applications requiring precise force control in industrial and mechanical tasks․
Hand-Operated Hydraulic Presses
Hand-operated hydraulic presses are compact, portable tools that rely on manual effort to generate hydraulic pressure․ They are widely used in metalworking, plastics processing, and assembling small parts․ These presses are ideal for applications requiring precise force control and are favored for their ease of use and versatility․ They are particularly suited for low to medium-duty tasks, offering a cost-effective solution for workshops and industries needing reliable, efficient pressing capabilities without the need for advanced automation or large-scale machinery․
Foot-Operated Hydraulic Presses
Foot-operated hydraulic presses utilize a foot pedal to generate hydraulic pressure, offering greater force and efficiency compared to hand-operated models․ These presses are ideal for applications requiring consistent and higher pressure, such as metal forming, bending, and pressing larger components․ Their design allows for hands-free operation, enabling precise control over the workpiece․ Foot-operated presses are popular in industrial settings due to their productivity and durability, making them a reliable choice for medium to heavy-duty tasks that demand precise and powerful pressing capabilities․
Key Components of a Manual Hydraulic Press
A manual hydraulic press consists of a hydraulic pump, cylinders, pistons, and a durable frame․ These components work together to generate and apply controlled force efficiently․
Hydraulic Pump and Its Function
The hydraulic pump is the core of a manual hydraulic press, converting mechanical energy into hydraulic pressure․ It drives the pistons, enabling precise force application․ Hand or foot operation allows efficient pressure generation, crucial for metal forming and assembly․ Durable and reliable, these pumps ensure consistent performance in various industrial settings, essential for the press’s functionality and effectiveness;
Cylinders and Pistons: Design and Operation
The cylinders and pistons in a manual hydraulic press are designed to withstand high pressures and ensure smooth operation․ Constructed from durable materials, they convert hydraulic pressure into mechanical force․ The pistons move within the cylinders, driven by pressurized fluid, enabling precise control․ Tight seals prevent fluid leakage, ensuring efficiency․ The design allows for consistent force application, essential for pressing operations․ Regular maintenance, like cleaning and inspecting seals, is crucial for optimal performance and longevity․
Applications of Manual Hydraulic Presses
Manual hydraulic presses are widely used in metalworking, machining, automotive, and aerospace industries for pressing, shaping, and assembling components with precise control and force․
Metalworking and Machining
Manual hydraulic presses are essential in metalworking and machining for bending, shaping, and assembling metal components․ Their portability and precise control make them ideal for pressing, punching, and forming metal parts․ Common applications include fitting bearings, bending metal sheets, and flattening surfaces․ These presses are also used in repair and maintenance tasks, offering a reliable solution for shaping and aligning metal pieces with minimal effort․ Their compact design allows easy use in workshops and job sites, making them indispensable for metal fabrication․
Plastics and Composite Material Processing
Manual hydraulic presses are widely used in plastics and composite material processing for thermoforming, laminating, and bonding․ Their controlled force and precise pressure application ensure uniform results․ These presses are ideal for shaping plastic sheets, molding composites, and assembling lightweight materials․ Compact and easy to operate, they are perfect for small-scale production and prototyping․ The ability to apply consistent pressure makes them essential for achieving high-quality finishes in plastic and composite fabrication, enhancing both efficiency and productivity in manufacturing processes․
Maintenance and Repair of Manual Hydraulic Presses
Regular maintenance ensures optimal performance and longevity․ Check hydraulic fluid levels, inspect for leaks, and clean the press regularly․ Lubricate moving parts and replace worn components promptly․
Regular Maintenance and Inspection
Regular maintenance is crucial for ensuring the longevity and efficiency of manual hydraulic presses․ Daily inspections should include checking hydraulic fluid levels, looking for signs of leaks, and ensuring all components are clean․ Weekly, lubricate moving parts and test the press under load to identify any irregularities․ Monthly, inspect the hydraulic pump, cylinders, and pistons for wear or damage․ Replace seals or filters as needed, and maintain proper alignment of the press components to prevent uneven stress․ Annual servicing by a professional is recommended to address complex issues and ensure optimal performance․
Safety Considerations for Manual Hydraulic Presses
Always wear protective gear, ensure proper training, and follow manufacturer guidelines to minimize risks and prevent accidents while operating manual hydraulic presses․
Operating Safety Tips and Precautions
Always wear protective gear, including gloves and safety glasses, when operating a manual hydraulic press․ Ensure proper training and follow manufacturer guidelines to avoid accidents․ Keep the workspace clean and well-lit to prevent slipping or tripping hazards․ Avoid overloading the press, as this can lead to equipment failure․ Regularly inspect hydraulic lines and components for leaks or damage․ Never operate the press while fatigued or distracted․ Use the correct tools and ensure all parts are securely positioned before pressing․ Be prepared for emergencies by having a first aid kit nearby and knowing proper shutdown procedures․
Comparison with Other Types of Presses
Manual hydraulic presses are often compared to automatic and mechanical presses, offering advantages in portability and cost-effectiveness for small-scale operations․
Manual Hydraulic Press vs․ Automatic Hydraulic Press
A manual hydraulic press relies on human effort to operate, offering portability and cost-effectiveness for small-scale tasks․ In contrast, an automatic hydraulic press uses advanced automation, enabling faster and more efficient operation for large-scale industrial applications․ While manual presses are ideal for precision and simplicity, automatic presses excel in high-volume production, reducing labor costs and increasing productivity․ Both presses serve distinct purposes, catering to different industrial needs and operational scales․
Advantages and Benefits of Manual Hydraulic Presses
Manual hydraulic presses are cost-effective, portable, and easy to use, making them ideal for small-scale operations and workshops with limited space and budget constraints․
Cost-Effectiveness and Portability
Manual hydraulic presses are highly cost-effective, offering an affordable solution for pressing needs without requiring significant investment in automated systems․ Their compact design makes them portable, allowing easy transportation to different workstations or job sites․ This portability is particularly advantageous in small workshops or remote locations where space and resources are limited․ Additionally, their low maintenance requirements further reduce operational costs, making them a practical choice for businesses seeking efficient and economical pressing solutions․ Their durability ensures long-term value, enhancing overall cost-effectiveness․
- Compact and lightweight for easy mobility․
- Lower initial and maintenance costs compared to automatic presses․
- Ideal for small-scale operations and remote applications․
Future Trends in Manual Hydraulic Press Technology
Advancements in manual hydraulic press technology include integration of advanced materials, compact designs, and smart automation features, enhancing efficiency and reducing operator effort in industrial applications․
- Lightweight yet durable materials for portability․
- Smart sensors for real-time pressure monitoring․
- Energy-efficient designs to minimize operational costs․
Integration of Advanced Materials and Automation
The integration of advanced materials and automation in manual hydraulic presses enhances performance, durability, and efficiency․ Modern presses now incorporate lightweight yet robust materials, reducing weight without compromising strength․ Automation features, such as programmable controls and smart sensors, enable precise pressure control and real-time monitoring, improving accuracy and reducing manual intervention․ These advancements also contribute to energy efficiency, making manual hydraulic presses more environmentally friendly and cost-effective for industrial and small-scale applications alike․
- Lightweight materials for improved portability․
- Smart sensors for real-time pressure monitoring․
- Programmable controls for customized operations․
- Cost-effective and portable design․
- Wide range of industrial applications․
- Potential for future technological enhancements․
Related posts:
Get your comprehensive hydraulic press manual for free! Learn operation, maintenance, and troubleshooting with our easy-to-follow guide.
Posted in Manuals